Transformation in an engineering enterprise through 5S. The implementation of 5S is implemented as a project, which facilitates change in our customers. In mechanical engineering, where different machines and individual jobs create a challenging environment, The accumulation of unnecessary items and dirt often leads to chaos. Without a well-established 5S system or practices, this can lead to inefficiency and unsafe working conditions. Lean.bg consultants, assisted an engineering enterprise to overcome these challenges through the successful implementation of 5S.
How We Achieved Change
1. Support from Senior Management
One of the key prerequisites for the success of the project was the clear will and support from the top management. They provided all the necessary resources and actively supported all stages of the implementation.
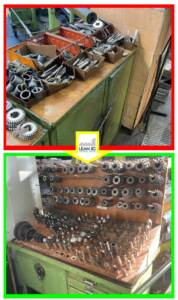
2.Motivation and Engagement of Teams
Leaders of teams and 5S areas showed a strong desire and motivation to implement the improvements. All workers actively participated in the process, which was a key factor in the success of the project.
Implementation Process
Formation of 5S Teams
At the beginning of the project, the management established a special 5S management team. Together with them, we divided the enterprise into different 5S zones and appointed leaders for each zone. We conducted trainings for all managers and operators, to ensure clarity and consistency in the application of the methodology.
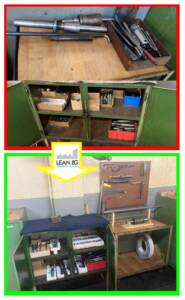
Initial Audits and Tasks
We visited all areas and performed an initial audit with a checklist, standardized by us. Together with the leaders, we set initial tasks to remove unnecessary items and clean the areas.
System Arrangement and Organization
Within three months, we conducted three more audits of each zone. We designed and implemented to create systems for arrangement and organization of tools and equipment. Leaders and operators themselves developed solutions to optimize workplaces. They designed instrument panels, shelf organization and other improvements, and the management provided them with support for the production.
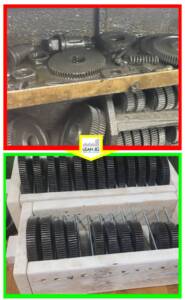
Results and Benefits
With this project, the enterprise achieved significant improvements in efficiency, cleanliness and organization of workplaces. The implementation of 5S increased productivity and improved the working environment, resulting in greater employee satisfaction.

Are you ready for a Transformation??
If you also want to transform your enterprise and achieve better efficiency and organization, Contact us. Our team of experts will help you implement 5S and other Lean methodologies, to achieve outstanding results.
If you are interested in systematic training on the 5S methodology – look here.